Коррозия металлов вред и польза
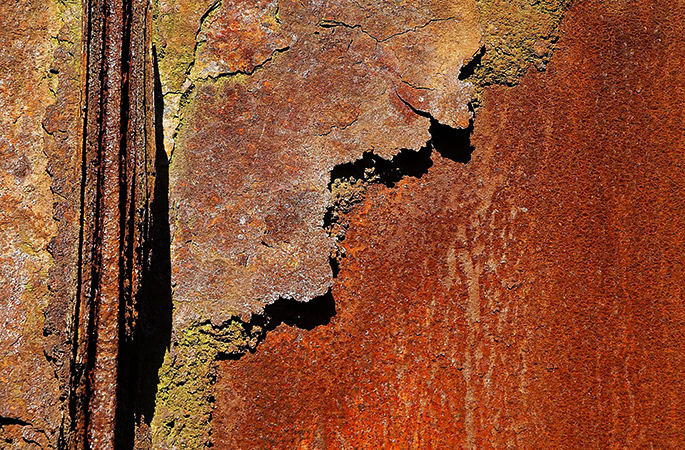
Многие люди хотя бы иногда любуются зеленоватым налетом на меди, или огорчаются потемнением серебряного украшения, или негодуют от появления ржавчины на поверхности автомобиля. Но не все понимают, что эти изменения цвета вызваны одним и тем же явлением – коррозией. Что же это такое?
Что такое коррозия металлов?
Коррозия металла ‑ это разрушение его поверхности из-за химического или электрохимического влияния внешней (коррозийной) среды.
Железо и его сплавы вступают в реакцию с кислородом и водой. В результате на их поверхностях рождаются оксиды Fe2O3 х nH2O и метагидроксиды железа FeO(OH) и Fe(OH)3, которые назвали ржавчиной. Процесс необратим и проникает в металл все глубже, продолжаясь до тех пор, пока изделие полностью не разрушится.
Корродируют и другие металлы, и их сплавы. Но в отличие от слоя ржавчины, оксиды, образовавшиеся на поверхности этих материалов, препятствуют их дальнейшему повреждению.
Известны 2 вида коррозии: химическая, электрохимическая. Первая возникает под влиянием сухих газов и неэлектролитов. Вторая – вследствие контакта с растворами-электролитами, содержащими ионы, она вызывает электрический ток. Температура ускоряет протекание процесса.
Плюсы
- Устойчивый краситель (Е 172). Применяют для окрашивания керамики, цемента и пищевых продуктов (выпечки, паштетов, конфет, рыбьей икры). Воздействуя щелочами, прокаливанием или водяным паром, получают порошки желтого, красного и черного цвета. Смешиванием получают оранжевый и коричневый цвета.
- Использование сверхпроводимости. При взаимодействии с железом воздуха с небольшим содержанием кислорода возникает медленно тянущаяся реакция образования черной ржавчины Fe3O4. Это ферромагнетик, который имеет свойство намагничиваться без внешнего магнитного поля, что используется для производства сверхпроводников.
- Применение в источниках тока. Используется электролитическая коррозия. Металл с отрицательным потенциалом (анод) помещают в водный раствор электролита (кислоты, соли, щелочи). Он отдает жидкости положительные ионы и постепенно растворяется. На катоде, имеющем положительный заряд, электроны собираются, а потом переходят во внешнюю среду. Чем ниже у металла электродный потенциал, тем быстрее он корродирует, отдавая ионы в раствор. Драгоценные металлы из-за их стойкости к коррозии наносят на контакты электросхем, платину используют в космических кораблях.
- Легирование. Металлом, у которого ниже электродный потенциал (например, алюминием или цинком), жертвуют для защиты железа, стали или другого металла. «Жертву» наносят сверху на другой материал, и она препятствует разрушению до тех пор, пока сама не будет полностью изъедена коррозией.
- Экономия средств на утилизацию. Постепенное превращение железного мусора в порошок происходит естественным образом. Не требуется дополнительных усилий для утилизации.
- Способствует рождению и применению изобретений. Люди придумывают новые инструменты и средства для избавления от ржавчины. Например, появились пескоструйные и дробеструйные пистолеты для механической очистки, промышленные очистители-спреи, гидропескоструйный эжектор.
Минусы
- Неэстетический вид. Вид покрытых ржавчиной трубопроводов вызывает отвращение, а ржавые инструменты некомфортно держать в руках. Побывав на практике в доме или в «горячем» цехе с сильно запущенными коммуникациями, некоторые учащиеся разочаровываются в будущей профессии. Страна теряет несостоявшихся слесарей, электромонтеров, монтажников и представителей других рабочих профессий, кому пришлось бы работать с «железом».
- Снижение продаж. Покупатели отказываются от покупки автомобилей, при осмотре которых замечают «следы» коррозии. В такси, имеющее на корпусе пятна ржавчины, неприятно садиться. Поэтому бывают случаи ухода пассажиров в другие таксомоторные фирмы, где автомобили выглядят не только чище, но и без коррозионных поражений.
- Потеря прочности. Здания и строения для химических производств часто строят из железобетона. Металлическая арматура в виде стержней, сеток или каркаса вставляется в бетон, чтобы повысить прочность и другие характеристики состава. Но стены снаружи и внутри таких помещений испытывают повышенные температуры, содержание в воздухе паров влаги и активных химических веществ, что значительно ускоряет осуществление коррозионных процессов. Такие строения требуют повышенной защиты, поэтому на арматуру наносят лакокрасочные или полимерные материалы, или легирующий металл. При этом легирование можно усилить нанесением пленочного или лакокрасочного, футеровочного или облицовочного слоя.
- Экологический вред и аварии. Разрушение трубопроводов приводит к утечке газа и нефтепродуктов, других химических веществ. Следовательно, загрязняется природная среда, возникают аварийные ситуации. Поэтому важно своевременно отыскивать дефекты в оборудовании и предотвращать негативные эффекты.
- Изношенность водопроводов ЖКХ. Эксперты утверждают, что стальные трубы служат в 3-4 раза меньше нормативного срока, что происходит из-за отсутствия надежной гидроизоляции. Катастрофическое состояние подземных трубопроводов влияет на ухудшение свойств питьевой воды и эпидемиологической обстановки (очаги тяжелых желудочных, кишечных заболеваний, гепатита). Низкое качество покрытий и недостаточный контроль за состоянием радиаторов отопления приводит к протечкам, из-за которых случаются ожоги населения, порча напольных покрытий и мебели, затопления нижерасположенных помещений.
- Человеческие жертвы. В разных странах из-за проржавевших металлоконструкций значительно снижается устойчивость мостов, что служит одной из причин их обрушения. В результате полного или частичного падения переправ получают ранения и погибают люди.
- Экономический ущерб. По мнению экспертов, потери от коррозии и расходы на борьбу с нею в экономически развитых странах оцениваются в среднем как 3 % ВНП.
Вывод
У коррозии есть положительные моменты. Например, есть повод купить новую плиту или другую бытовую технику, а также кухонную утварь, когда они заржавеют. Поскольку если коррозионных проявлений нет, то многим жалко выкидывать старые вещи. Но ущерб от коррозийных поражений такой катастрофический, что необходимо защищаться от них.
Источник
Может ли коррозия приносить пользу?
Для подтверждения положительных сторон этого явления изучите следующие факты.
При термической обработке стальные листы покрываются тонким трудно отделяемым слоем окалины. Таким листам дают слегка поржаветь, после чего они легко очищаются от окалины.
У древних горцев существовал особый секрет приготовления сверхпрочных и острых клинков, которые легко разрубали не только ткани, но и сухожилия и кости. Изделия на несколько лет закапывали в землю, после специальной обработки поржавевших клинков они приобретали высокую прочность.
Любопытную технологию превращения слоя ржавчины в… защитное покрытие удалось разработать индийским ученым. Для этого на стальное изделие, покрытое густым налетом ржавчины, наносят специальный состав, благодаря которому слой оксидов становится прочным панцирем черного цвета. Затем на него наносят краску, которая, кстати, держится на этом защитном слое надежнее, чем непосредственно на металлической поверхности. Теперь изделию коррозия не страшна.
Существует электрохимическая размеренная обработка металлов. В специально подобранном электролите ток энергично растворяет металл (металл корродирует). Вместо резца используется направленное электрическое поле. Задача, как у скульптора, — убрать все лишнее. За короткое время на наших глазах возникает профиль детали. Причем чистота обработки, очень высокая, скорости в 5—15 раз быстрее резания.
В технике нашла применение и сама ржавчина как защитное средство. Например, освоена выплавка низколегированных сталей с малым содержанием никеля, хрома и меди. Подобная сталь быстро ржавеет, но под слоем опавшей ржавчины остается плотная черная пленка, которая крепко сцепляется с металлом и практически полностью защищает его от дальнейшей коррозии. Время, необходимое для образования защитного слоя, колеблется от двух до четырех лет. После этого скорость коррозии уменьшается и составляет от 2 до 35 мк в год в зависимости, от условий. В обычных условиях лист из такой стали проржавел бы лишь на 0,3 мм.
В 1834 г. в «Горном журнале» была опубликована статья «Улучшение железа и стали посредством ржавления в земле». Способ превращения железа в сталь через ржавление в земле известен людям с глубокой древности. Например, черкесы на Кавказе закапывали полосовое железо в землю, а откопав его через 10— 15 лет, выковывали из него свои сабли, которые могли перерубить даже ружейный ствол, щит, кости врага. В земле железо, естественно, ржавело, превращаясь в метагидроксид железа, но одновременно насыщалось углеродом и азотом при контакте с различными органическими веществами почвы.
Ржавчина обладает хорошей сорбционной способностью к различным органическим веществам. После выкапывания ржавое железо вместе с органическими веществами нагревали в горнах, ковали, а затем охлаждали водой — закаливали. Углерод и азот появлялись в поверхностном слое откованного металла, упрочняя его и сообщая ему особую твердость. В слое при термической обработке образуется очень твердое соединение: карбид железа Fe3С — цементит. Впоследствии для получения твердой стали вместо длительного пребывания железа в земле перешли к плавке железа под слоем древесного угля.
Источник: «Химия в школе»
Источник
Корро́зия — это самопроизвольное разрушение металлов и сплавов в результате химического, электрохимического или физико-химического взаимодействия с окружающей средой. Разрушение по физическим причинам не является коррозией, а характеризуется понятиями «эрозия», «истирание», «износ».
Причиной коррозии служит термодинамическая неустойчивость конструкционных материалов к воздействию веществ, находящихся в контактирующей с ними среде.
Пример — кислородная коррозия железа в воде:
Гидроксид железа Fe(OH)3 и является тем, что называют ржавчиной.
В повседневной жизни для сплавов железа (сталей) чаще используют термин «ржавление» — коррозия железа и его сплавов с образованием продуктов коррозии, состоящих из гидратированных остатков железа.
На неметаллические материалы определение коррозии не распространяется. Применительно к полимерам существует понятие «старение», аналогичное термину «коррозия» для металлов. Например, старение резины из-за взаимодействия с кислородом воздуха или разрушение некоторых пластиков под воздействием атмосферных осадков, а также биологическая коррозия.
Скорость коррозии, как и всякой химической реакции, очень сильно зависит от температуры. Повышение температуры на 100 градусов может увеличить скорость коррозии на несколько порядков.
Классификация видов коррозии[править | править код]
Неравномерная атмосферная коррозия
Коррозионные процессы отличаются широким распространением и разнообразием условий и сред, в которых они протекают. Поэтому пока нет единой и всеобъемлющей классификации встречающихся случаев коррозии[1].
По типу агрессивных сред, в которых протекает процесс разрушения, коррозия может быть следующих видов:
- газовая коррозия;
- атмосферная коррозия;
- коррозия в неэлектролитах;
- коррозия в электролитах;
- подземная коррозия;
- биокоррозия;
- коррозия под воздействием блуждающих токов.
По условиям протекания коррозионного процесса различаются следующие виды:
- контактная коррозия;
- щелевая коррозия;
- коррозия при неполном погружении;
- коррозия при полном погружении;
- коррозия при переменном погружении;
- коррозия при трении;
- межкристаллитная коррозия;
- коррозия под напряжением.
По характеру разрушения:
- сплошная коррозия, охватывающая всю поверхность:
- равномерная;
- неравномерная;
- избирательная;
- локальная (местная) коррозия, охватывающая отдельные участки:
- пятнами;
- язвенная;
- точечная;
- сквозная;
- межкристаллитная (расслаивающая в деформированных заготовках и ножевая в сварных соединениях).
Главная классификация производится по механизму протекания процесса. Различают два вида:
- химическую коррозию;
- электрохимическую коррозию.
Коррозия неметаллических материалов[править | править код]
По мере ужесточения условий эксплуатации (повышение температуры, механических напряжений, агрессивности среды и др.) и неметаллические материалы подвержены действию среды. В связи с чем термин «коррозия» стал применяться и по отношению к этим материалам, например «коррозия бетонов и железобетонов», «коррозия пластмасс и резин». При этом имеется в виду их разрушение и потеря эксплуатационных свойств в результате химического или физико-химического взаимодействия с окружающей средой. Но следует учитывать, что механизмы и кинетика процессов для неметаллов и металлов будут разными.
Коррозия металлов[править | править код]
Ржавчина, самый распространённый вид коррозии.
Если цепь велосипеда не смазывать, она ржавеет и ржавчина распространяется на звёзды
Коррозия металлов — разрушение металлов вследствие химического или электрохимического взаимодействия их с коррозионной средой[2]. Для процесса коррозии следует применять термин «коррозионный процесс», а для результата процесса — «коррозионное разрушение».
Под коррозией понимают происходящее на поверхности электрохимическое или химическое разрушение металлического материала. Наиболее часто при коррозии металл окисляется с образованием ионов металла, которые при дальнейших превращениях дают различные продукты коррозии. Коррозия может быть вызвана как химическим, так и электрохимическим процессом. Соответственно, различают химическую и электрохимическую коррозию металлов.
Типы коррозии[править | править код]
Различают 4 основных вида коррозии: электрохимическая коррозия, водородная, кислородная коррозия и химическая.
Электрохимическая коррозия[править | править код]
Разрушение металла под воздействием возникающих в коррозионной среде гальванических элементов называют электрохимической коррозией. При электрохимической коррозии всегда требуется наличие электролита (Конденсат, дождевая вода и т. д.), с которым соприкасаются электроды — либо различные элементы структуры материала, либо два различных соприкасающихся материала с различающимися окислительно-восстановительными потенциалами. Если в воде растворены ионы солей, кислот, или т. п., электропроводность её повышается, и скорость процесса увеличивается.
При соприкосновении двух металлов с различными окислительно-восстановительными потенциалами и погружении их в раствор электролита, например, дождевой воды с растворенным углекислым газом CO2, образуется гальванический элемент, так называемый коррозионный элемент. Он представляет собой не что иное, как замкнутую гальваническую ячейку. В ней происходит медленное растворение металлического материала с более низким окислительно-восстановительным потенциалом; второй электрод в паре, как правило, не корродирует. Этот вид коррозии особо присущ металлам с высокими отрицательными потенциалами. Так, совсем небольшого количества примеси на поверхности металла с большим редокс-потенциалом уже достаточно для возникновения коррозионного элемента. Особо подвержены риску места соприкосновения металлов с различными потенциалами, например, сварочные швы или заклёпки.
Если растворяющийся электрод коррозионно-стоек, процесс коррозии замедляется. На этом основана, например, защита железных изделий от коррозии путём оцинковки — цинк имеет более отрицательный потенциал, чем железо, поэтому в такой паре железо восстанавливается, а цинк должен корродировать. Однако в связи с образованием на поверхности цинка оксидной плёнки процесс коррозии сильно замедляется.
Примером крупномасштабной электрохимической коррозии может служить происшествие, случившееся в декабре 1967 года с норвежским рудовозом «Анатина»[3] (англ. Anatina), следовавшим из Кипра в Осаку. Налетевший в Тихом океане тайфун привёл к попаданию в трюмы солёной воды и образованию большой гальванической пары: медного концентрата со стальным корпусом судна, который вскоре размягчился, и судно подало сигнал бедствия. Экипаж был спасён подоспевшим немецким судном, а сама «Анатина» еле-еле добралась до порта[4][5].
Водородная и кислородная коррозия
Если происходит восстановление ионов H3O+ или молекул воды H2O, говорят о водородной коррозии или коррозии с водородной деполяризацией. Восстановление ионов происходит по следующей схеме:
или
Если водород не выделяется, что часто происходит в нейтральной или сильно щелочной среде, происходит восстановление кислорода и здесь говорят о кислородной коррозии или коррозии с кислородной деполяризацией:
Коррозионный элемент может образовываться не только при соприкосновении двух различных металлов. Коррозионный элемент образуется и в случае одного металла, если, например, структура его поверхности неоднородна (например, межкристаллитная коррозия).
Химическая коррозия[править | править код]
Химическая коррозия — взаимодействие поверхности металла с коррозионно-активной средой, не сопровождающееся возникновением электрохимических процессов на границе фаз. В этом случае взаимодействия окисления металла и восстановление окислительного компонента коррозионной среды протекают в одном акте. Например, образование окалины при взаимодействии материалов на основе железа при высокой температуре с кислородом:
Виды коррозии[править | править код]
- Послойная коррозия
- Нитевидная коррозия
- Структурная коррозия
- Межкристаллитная коррозия
- Избирательная коррозия
- Графитизация чугуна
- Обесцинкование
- Щелевая коррозия
- Ножевая коррозия
- Коррозионная язва
- Коррозионное растрескивание
- Коррозия под напряжением
- Коррозионная усталость
- Предел коррозионной усталости
- Коррозионная хрупкость
Борьба с коррозией[править | править код]
Коррозия приводит ежегодно к миллиардным убыткам, и решение этой проблемы является важной задачей. Основной ущерб, причиняемый коррозией, заключается не в потере металла как такового, а в огромной стоимости изделий, разрушаемых коррозией. Вот почему ежегодные потери от неё в промышленно развитых странах столь велики. Истинные убытки от неё нельзя определить, оценив только прямые потери, к которым относятся стоимость разрушившейся конструкции, стоимость замены оборудования, затраты на мероприятия по защите от коррозии. Ещё больший ущерб составляют косвенные потери. Это простои оборудования при замене прокорродировавших деталей и узлов, утечка продуктов, нарушение технологических процессов.
Идеальная защита от коррозии на 80 % обеспечивается правильной подготовкой поверхности, и только на 20 % качеством используемых лакокрасочных материалов и способом их нанесения[6]. Одним из наиболее производительных и эффективных методов подготовки поверхности перед дальнейшей защитой субстрата является пескоструйная обработка.
Обычно выделяют три направления методов защиты от коррозии:
- Конструкционный
- Активный
- Пассивный
Для предотвращения коррозии в качестве конструкционных материалов применяют нержавеющие стали, кортеновские стали, цветные металлы.
При добавлении небольшого количества хрома в сталь на поверхности металла образуется оксидная плёнка. Содержание хрома в нержавеющей стали — более 12 процентов.
При проектировании конструкции стараются максимально изолировать от попадания коррозионной среды, применяя клеи, герметики, резиновые прокладки.
Активные методы борьбы с коррозией направлены на изменение структуры двойного электрического слоя. Применяется наложение постоянного электрического поля с помощью источника постоянного тока, напряжение выбирается с целью повышения электродного потенциала защищаемого металла. Другой метод — использование жертвенного анода, более активного материала, который будет разрушаться, предохраняя защищаемое изделие.
Кислородная коррозия оцинкованного железа
Кислородная коррозия железа, покрытого оловом
Красочное покрытие, полимерное покрытие и эмалирование должны, прежде всего, предотвратить доступ кислорода и влаги. Часто также применяется покрытие, например, стали другими металлами, такими как цинк, олово, хром, никель. Цинковое покрытие защищает сталь даже когда покрытие частично разрушено. Цинк имеет более отрицательный потенциал и корродирует первым. Ионы Zn2+ токсичны. При изготовлении консервных банок применяют жесть, покрытую слоем олова. В отличие от оцинкованной жести, при разрушении слоя олова корродировать, притом усиленно, начинает железо, так как олово имеет более положительный потенциал. Другая возможность защитить металл от коррозии — применение защитного электрода с большим отрицательным потенциалом, например, из цинка или магния. Для этого специально создаётся коррозионный элемент. Защищаемый металл выступает в роли катода, и этот вид защиты называют катодной защитой. Растворяемый электрод, называют, соответственно, анодом протекторной защиты. Этот метод применяют для защиты от коррозии морских судов, мостов, котельных установок, расположенных под землей труб. Для защиты корпуса судна на наружную сторону корпуса крепят цинковые пластинки.
Если сравнить потенциалы цинка и магния с железом, они имеют более отрицательные потенциалы. Но тем не менее корродируют они медленнее вследствие образования на поверхности защитной оксидной плёнки, которая защищает металл от дальнейшей коррозии. Образование такой плёнки называют пассивацией металла. У алюминия её усиливают анодным окислением (анодирование).
Газотермическое напыление[править | править код]
Для борьбы с коррозией используют также методы газотермического напыления. С помощью газотермического напыления на поверхности металла создается слой из другого металла/сплава, обладающий более высокой стойкостью к коррозии (изолирующий) или наоборот менее стойкий (протекторный). Такой слой позволяет остановить коррозию защищаемого металла. Суть метода такова: газовой струей на поверхность изделия на огромной скорости наносят частицы металлической смеси, например цинк, в результате чего образуется защитный слой толщиной от десятков до сотен микрон. Газотермическое напыление также применяется для продления жизни изношенных узлов оборудования: от восстановления рулевой рейки в автосервисе до агрегатов нефтедобывающих компаний[7].
Термодиффузионное цинковое покрытие[править | править код]
Для эксплуатации металлоизделий в агрессивных средах необходима более стойкая антикоррозионная защита поверхности металлоизделий. Термодиффузионное цинковое покрытие является анодным по отношению к чёрным металлам и электрохимически защищает сталь от коррозии. Оно обладает прочным сцеплением (адгезией) с основным металлом за счет взаимной диффузии железа и цинка в поверхностных интерметаллидных фазах, поэтому не происходит отслаивания и скалывания покрытий при ударах, механических нагрузках и деформациях обработанных изделий[8].
Диффузионное цинкование, осуществляемое из паровой или газовой фазы при высоких температурах (375—850 °C), или с использованием разрежения (вакуума) — при температуре от 250 °C, применяется для покрытия крепёжных изделий, труб, деталей арматуры и др. конструкций. Значительно повышает стойкость стальных, чугунных изделий в средах, содержащих сероводород (в том числе против сероводородного коррозионного растрескивания), промышленной атмосфере, морской воде и др. Толщина диффузионного слоя зависит от температуры, времени, способа цинкования и может составлять 0,01—1,5 мм. Современный процесс диффузионного цинкования позволяет образовывать покрытие на резьбовых поверхностях крепёжных изделий, без затруднения их последующего свинчивания. Микротвёрдость слоя покрытия Hμ = 4000 — 5000 МПа. Диффузионное цинковое покрытие также значительно повышает жаростойкость стальных и чугунных изделий при температуре до 700 °C. Возможно получение легированных диффузионных цинковых покрытий, применяемое для повышения их служебных характеристик.
Кадмирование[править | править код]
Покрытие стальных деталей кадмием производится методами, аналогичными цинкованию, но даёт более сильную защиту, особенно в морской воде. Применяется значительно реже из-за значительной токсичности кадмия и его дороговизны. Также покрывают тонким слоем оксида меди, что предотвращает дальнейшее размножение коррозии.
Хромирование[править | править код]
Покрытие стальных деталей хромом.
Экономический ущерб от коррозии[править | править код]
Экономические потери от коррозии металлов огромны. В США по последним данным NACE[9], ущерб от коррозии и затраты на борьбу с ней составили 3,1 % от ВВП (276 млрд долларов). В Германии этот ущерб составил 2,8 % от ВВП. По оценкам специалистов различных стран эти потери в промышленно развитых странах составляют от 2 до 4 % валового национального продукта. При этом потери металла, включающие массу вышедших из строя металлических конструкций, изделий, оборудования, составляют от 10 до 20 % годового производства стали[10].
Обрушение Серебряного моста.
Ржавчина является одной из наиболее распространённых причин аварий мостов. Так как ржавчина имеет гораздо больший объём, чем исходная масса железа, её наращивание может привести к неравномерному прилеганию друг к другу конструкционных деталей. Это стало причиной разрушения моста через реку Мианус[en] в 1983 году, когда подшипники кронштейна моста проржавели внутри. Три водителя погибли при падении в реку. Исследования показали, что сток дороги был перекрыт и не был почищен, а сточные воды проникли в опоры моста[11]. Согласно исследованию Национального совета по безопасности на транспорте, разрушение моста было вызвано механической поломкой наружного кронштейна, удерживающего пролёт моста и его обоих штифтов. Ржавчина образовалась в подшипнике штифта. А так как её объём всегда гораздо больше, нежели исходная стальная деталь, это привело к неравномерному прилеганию друг к другу частей конструкции. В случае с мостом, ржавая масса отодвинула внутренний кронштейн от конца штифта, скрепляющего между собой наружный и внутренний кронштейны. (При этом возникло усилие, превышающее проектные пределы для зажимов, удерживающих штифты!) Из-за этого вся масса пролёта переместилась на внешний кронштейн. Эта дополнительная нагрузка на него вызвала усталостную трещину в штифте. Когда два тяжелых грузовика въехали в данную секцию моста, штифты окончательно вышли из строя, и пролёт моста упал в реку…
15 декабря 1967 года Серебряный мост, соединяющий Пойнт Плезант, штат Западная Виргиния, и Канауга, штат Огайо, неожиданно рухнул в реку Огайо. В момент обрушения 37 автомобилей двигались по мосту, и 31 из них упали вместе с мостом. Сорок шесть человек погибли, и девять серьёзно пострадали. Помимо человеческих жертв и травм, был разрушен основной транспортный путь между Западной Виргинией и Огайо. Причиной обрушения стала коррозия[12].
Мост Кинзу в Пенсильвании был разрушен в 2003 году от торнадо прежде всего потому, что центральные основные болты проржавели, существенно снизив его устойчивость.
См. также[править | править код]
- Shewanella oneidensis
- Старение материалов
Примечания[править | править код]
- ↑ Антикоррозионная защита / Козлов Д.Ю.. — Екатеринбург: ООО «ИД «Оригами», 2013. — С. 343. — 440 с. — 1000 экз. — ISBN 978-5-904137-05-2.
- ↑ «ГОСТ 5272-68: Коррозия металлов. Термины.»
- ↑ Спиридонов А. А. В служеньи ремеслу и музам. — 2-е изд. — М.: Металлургия, 1989. — С. 53. — (Научно-популярная библиотека школьника). — 50 000 экз. — ISBN 5-229-00355-3.
- ↑ Merchant and Navy Ship events (1946—2000) — 25/12 1967 (недоступная ссылка). Дата обращения 11 августа 2014. Архивировано 16 февраля 2012 года.
- ↑ См. также, например, газеты «Ogden Standard Examiner», «Bridgeport Post» за 24 декабря 1967 года.
- ↑ ISO 8501-1. «Подготовка стальной основы перед нанесением красок и подобных покрытий. Визуальная оценка чистоты поверхности Часть 1. Степени окисления и степени подготовки непокрытой стальной основы и стальной основы после полного удаления прежних покрытий.»
- ↑ Газотермическое напыление (недоступная ссылка)
- ↑ ГОСТ Р 9.316-2006 «Единая система защиты от коррозии и старения. Покрытия термодиффузионные цинковые. Общие требования и методы контроля.
- ↑ Доклад на 16-м Всемирном конгрессе по коррозии в Пекине, сентябрь 2005 года.
- ↑ «Руководство для подготовки инспекторов по визуальному и измерительному контролю качества окрасочных работ» — Екатеринбург: ООО «ИД «Оригами», 2009—202 с., ISBN 978-5-9901098-1-5
- ↑ «Part Of Bridge On Route I-95 Falls Into River In Greenwich,; Killing 3.». New York Times. June 29, 1983. (англ.)
- ↑ ИЗ ИСТОРИИ КОРРОЗИИ (неопр.) // журнал «Очистка. Окраска». — 2008. — June (т. № 4 (15)). — С. 48.
Литература[править | править код]
- Красноярский В. В., Френкель Г. Я., Носов Р. П. Коррозия и защита металлов. — М.: Металлургия, 1969. — 299 с.
Ссылки[править | править код]
- Учебный фильм «Коррозия металлов» (Школфильм)
- Таблицы применимости материалов. Коррозионная стойкость материалов. Инженерный справочник DPVA
- Коррозия металлов, способы защиты от нее — учебный фильм, производство Центрнаучфильм.
Источник